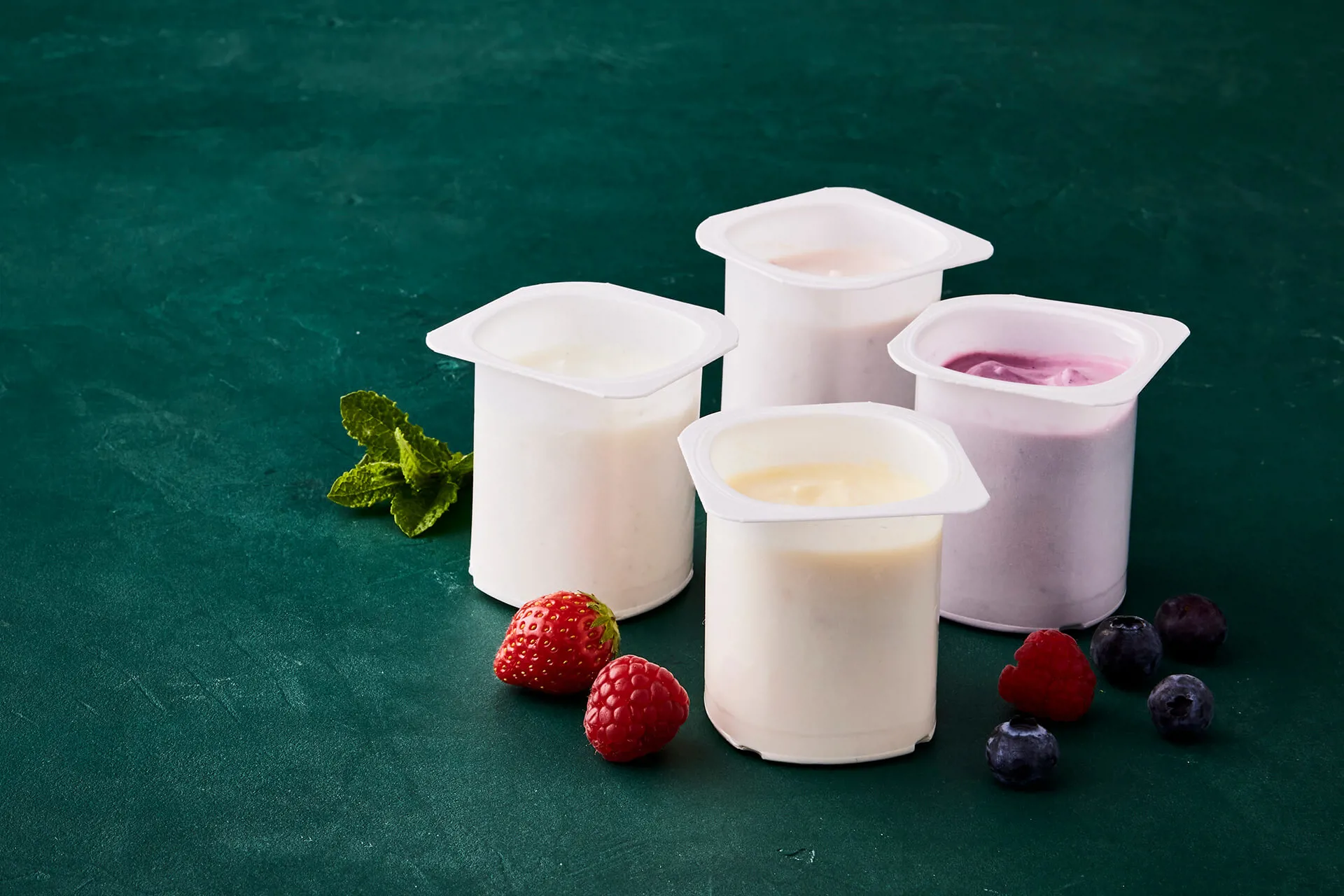
FEATURE ARTICLE
FEATURE ARTICLE
Efficiency, safety, sustainability and costs are key challenges for plastics compounders and converters to meet when adding specific properties and functions to base polymers. Pelletised masterbatches with plant-based food-grade Einar® products offer superior solutions over individual, paste, powder or liquid and synthetic additives.
The metering of additives to plastics in precise concentrations while achieving high homogeneity can be difficult without the right equipment and experience. This is where masterbatch providers come into play. With their expertise in blending different additives and with their flexible manufacturing capacities, they offer diverse and convenient solutions based on compatible carrier polymers. Supplied in pelletised form, these additive masterbatches are easy to handle without any safety issues and can be directly fed to film extrusion lines or injection moulding machines in exactly the required, effective and efficient concentration.
The most efficient of our Einar® plant-based polymer additives are available as pastes and develop their desired functions at rather low concentration levels. For many compounders and converters, however, it is rather difficult to achieve and control the consistency of those levels in order to maximise the economic benefit that can be gained from our additives. Rather than working with individual pastes or liquids, they rely on ready-to-use pelletised additive masterbatches.
Beyond efficiency, masterbatch manufacturers can add significant value to their products when selecting our additives for their formulations. Major reasons for switching to Einar® polymer additives also include their inherent safety and sustainability. As natural components derived exclusively from animal-free and edible plant sources such as palm, rapeseed, sunflower, coconut and other vegetable oils, they all have unconditional FDA and EU food contact approvals. This gives them an ideal fit in additive masterbatches for use in food packaging polymers while eliminating concerns associated with traditional fossil-based amines or amides.
Masterbatch providers can further differentiate their portfolio with Einar® as the world’s only brand of plant-based additives produced in fully carbon-neutral facilities, thus contributing to the reduction of the carbon footprint across the entire value chain from the raw materials to the end products. Moreover, the low concentrations and natural composition of our additives will not interfere with mechanical nor with chemical end-of-life recycling schemes in an emerging circular plastics economy. At the same time, they can enable thinner packaging without compromising food safety or electronic integrity.
In a market where the final products are being optimised to be mono-material or to use less material with the aim to increase recyclability and reduce resource consumption, thin-walled packaging and laminated films are gaining ground. These are demanding solutions in which a sufficient anti-stat or anti-fog coverage can be difficult to achieve. Here, our Einar® line of products can equip masterbatch producers with efficient solutions to meet their packaging customers’ needs.
The most typical Einar® products for incorporation in additive masterbatches include a diversified range of anti-static and anti-fogging grades, which are among the preferred sustainable choices for many packaging manufacturers and brands.
Einar® 601, our foremost anti-stat for polyethylene (PE) compounds, is a proven plant-based alternative to ethoxylated amines and lends highly effective anti-static performance to masterbatches for PE film and foam at loading levels as low as 0.1 to 0.4 per cent. At the same time, its long-term stability e.g. in LDPE-blown film exceeds that of petrol-based and less safe offerings, such as combinations of glycerol monostearates (GMS) with ethoxylated amines (EA).
Einar® 601 has a perfect market fit in formulations that must work well even under low humidity conditions and ensures smooth operation in high-speed filling lines for powdered products. While helping to prevent the attraction of dust on transparent food packaging surfaces, it also protects sensitive electronics packaging from static build-up that may result in detrimental electric discharges.
Similar anti-static properties can be provided in masterbatches for polypropylenes (PP) by Einar® 401 and Einar® 411, two unique glycerol ester blends with selected plant-based fatty acids, such as from coconut and segregated palm oil. Einar® 401 is specifically developed for impact copolymer PP and can also enhance the mould release of end products. In static decay testing, the additive has confirmed that it is able to outperform traditional GMS/EA offerings. Einar® 401 also works well in PP foams used in the packaging of electronic goods.
For PP film Einar® 411 offers excellent performance in a very broad range of applications. In most random and block copolymer films it will provide good and sufficient performance at low loading levels. In homopolymer, a highly crystalline material where anti-stat migration is low, anti-stat concentrations need to be in the higher end of the recommended loading level of 0.1 – 0.4%.
In coextruded or laminated packaging films, the anti-stat is often added to a very thin section of the entire film and therefore, the anti-stat must be a very reliable and efficient performer. Einar® 411 will deliver the performance you need and has proven to deliver excellent performance when used in the thinner film sections of a sealing layer.
On the anti-fog side, masterbatch manufacturers will find highly efficient solutions in Einar® 618 for PP and Einar® 611 for PE. Both products are polyglycerol esters (PGE) derived from vegetable oils. They prevent fogging from chilled or hot packaged food and keep food wrap films and other types of packaging transparent during cold storage. Building on the established benefits of Einar® 211 in food packaging, Einar® 611 performs exceptionally well in cold fog applications of co-extruded and laminated PE films, whereas Einar® 618 shows excellent cold fog and hot fog resistance also in cast PP and BOPP films. They are complemented by Einar® 422, a new hot fog development targeted particularly at microwave-ready meal packages.
These and further plant-based additives suitable for integration in safe, sustainable and cost-efficient masterbatches can be tested and compared at our Polymer Application Centre in Denmark. Masterbatch producers are also invited to request Einar® samples and will be supported by our specialists during masterbatch qualification as well as troubleshooting once implemented.
FEATURE ARTICLE
FEATURE ARTICLE
VIDEO FEATURE
FEATURE ARTICLE
TECHNICAL ARTICLE
VIDEO FEATURE
TECHNICAL ARTICLE
WHITEPAPER