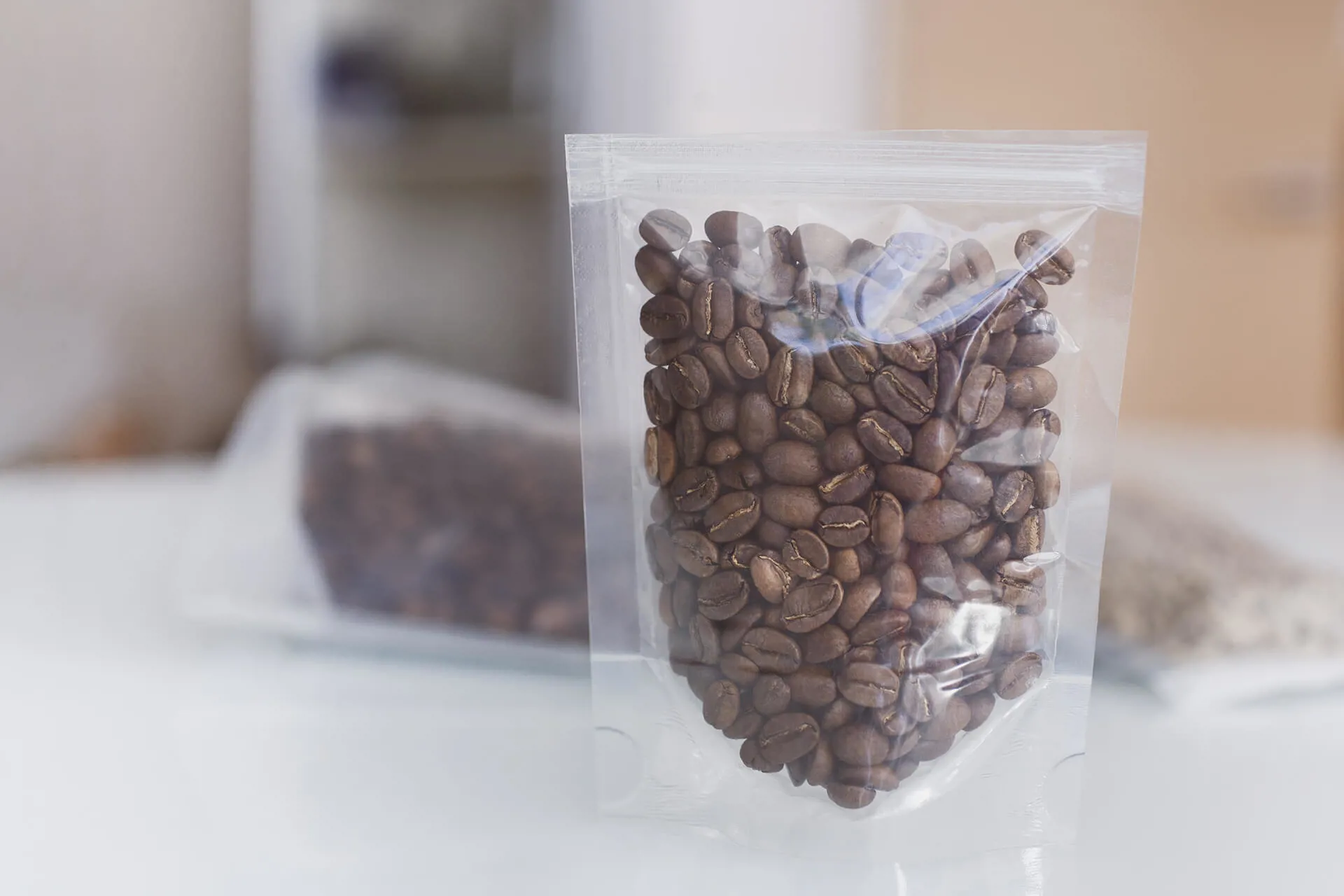
FEATURE ARTICLE
FEATURE ARTICLE
As manufacturers strive to reduce plastic usage and create more sustainable packaging, thinner co-extruded and laminated structures are becoming more common. However, thinner layers can pose challenges for anti-static protection.
This article discusses how to maintain effective anti-static properties in thinner packaging layers.
When utilising co-extruded and laminated PE film in a packaging solution, the anti-static agent is often included in the sealing layer. However, as manufacturers aim to minimise plastic usage and decrease the thickness of the layers, there is limited material available for the additive to effectively migrate to the packaging surface. This migration is crucial for ensuring efficient anti-static protection. Therefore, using thinner co-extruded and laminated structures for sustainability purposes can impact the effectiveness of migratory anti-static additives. These additives are typically integrated into a specific layer of the packaging material and gradually migrate to the surface over time to deliver anti-static properties.
Driven by their hydrophilic ends, the additive molecules in the polymer matrix migrate towards the polymer surfaces to act as surfactants e.g. against fogging and static build-up. The performance of migratory anti-static additives may be influenced by the reduced thickness of the packaging structure in several ways:
The reduced thickness of the packaging material may result in lower concentrations of the migratory anti-static additives on the surface. As the additives migrate, they accumulate on the surface, forming a layer that provides anti-static properties. Thinner structures may have lower overall additive concentration leading to a lower surface concentration, which could potentially impact the effectiveness of static dissipation.
The overall anti-static performance of the packaging material may be affected due to the reduced availability of anti-static additives. The anti-static properties are directly related to the concentration and distribution of the additive on the surface.
To mitigate these effects, it becomes crucial to carefully optimise the formulation and concentration of the anti-static additive for thinner layers. Manufacturers can select additives with higher migration rates or improved surface concentration characteristics to compensate for the limited amount available. They may also explore alternative anti-static technologies that can provide effective anti-static properties with lower additive concentrations, such as inherent static-dissipative materials or coatings.
Einar® 601 offers several advantages in the context of thin PE films:
Einar® 601 exhibits improved migration efficiency, allowing it to migrate readily through the thickness of the PE film, even in lower quantities. This efficient migration ensures that the additive can effectively reach the film’s surface, despite the reduced thickness of the layers. It helps achieve the desired anti-static properties at low concentrations and in a shorter timeframe.
Einar® 601 demonstrates excellent performance at lower dosage levels. It can provide effective anti-static properties even when used in reduced concentrations, which is advantageous when incorporating limited amounts of the additive into thinner PE film layers. The lower dosage requirement helps minimise costs and potential negative effects on other material properties.
Einar® 601 is specifically designed for compatibility with PE films. It integrates well with polyethylene and its various copolymers commonly used in co-extrusion and lamination processes. The additive’s compatibility ensures ease of formulation and integration into existing manufacturing processes without significant adjustments or adverse effects on the overall film performance.
By utilising Einar® 601 as an anti-static additive in thin PE films, manufacturers can overcome the limitations associated with thinner co-extruded and laminated structures while maintaining effective anti-static properties and static control. Its efficient migration, highly potent anti-stat chemistry, lower dosage requirement and compatibility with PE films contribute to reliable anti-static performance in the new innovative and less resource-intensive packaging solutions of the modern world.
Einar® 601 also has an excellent performance in LLDPE films and is the ideal anti-stat in an LLDPE metallocene sealing layer.
Palsgaard offers technical support and expertise to assist manufacturers in the proper utilisation of Einar® additives. This guidance ensures that manufacturers can effectively incorporate the additives into their production processes while maximising safety and performance.
FEATURE ARTICLE
TECHNICAL ARTICLE
FEATURE ARTICLE
FEATURE ARTICLE